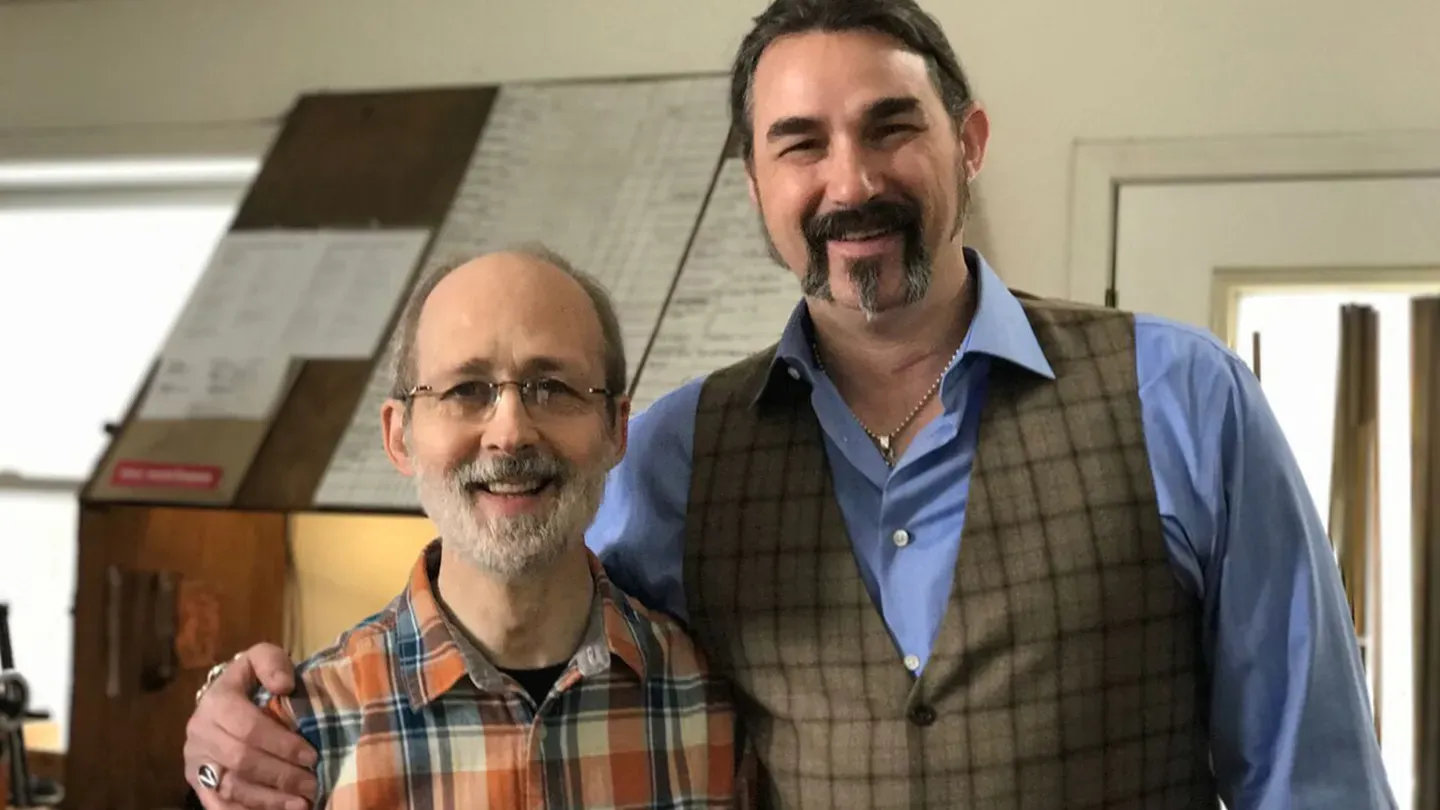
A Craftsman's Legacy
The Brass Horn Makers
Episode 406 | 26m 46sVideo has Closed Captions
Eric shines the brass with a master French horn maker.
Eric shines the brass with master French horn makers and musicians Rick and Celeste Seraphinoff.
Problems with Closed Captions? Closed Captioning Feedback
Problems with Closed Captions? Closed Captioning Feedback
A Craftsman's Legacy is presented by your local public television station.
Distributed nationally by American Public Television
A Craftsman's Legacy
The Brass Horn Makers
Episode 406 | 26m 46sVideo has Closed Captions
Eric shines the brass with master French horn makers and musicians Rick and Celeste Seraphinoff.
Problems with Closed Captions? Closed Captioning Feedback
How to Watch A Craftsman's Legacy
A Craftsman's Legacy is available to stream on pbs.org and the free PBS App, available on iPhone, Apple TV, Android TV, Android smartphones, Amazon Fire TV, Amazon Fire Tablet, Roku, Samsung Smart TV, and Vizio.
Providing Support for PBS.org
Learn Moreabout PBS online sponsorship♪♪♪ >> There's more than one way to leave a legacy.
For some, it means plaques, monuments, and halls of fame.
But for others, legacy comes from a place more simple.
>> You just snip off the ends.
♪♪♪ Okay, so, we're building a tepee shape.
>> The Ford F-150, a proud supporter of "A Craftsman's Legacy."
♪♪♪ >> Sometimes it's the simple designs that escape me.
For instance, I've never really thought about why there's so many bends in brass horns.
I'm sure there's a purpose outside of just being cool.
I'm in Indiana visiting Rick Seraphinoff.
Rick is not only a fine craftsman, he's also a historian and a professional musician.
I'm pretty certain Rick's gonna be able to answer any questions I have about horns.
♪♪♪ A craftsman battles for perfection, never willing to give in or walk away.
I'm Eric Gorges.
I build custom motorcycles using skills passed on by countless generations before me.
I used to work 9:00 to 5:00, chasing money and titles, and it nearly broke me.
So, I started over.
I decided to work with my hands to feed my soul.
Please join me on a quest to uncover the skills that built our society.
We'll discover what drives the men and women who I call my heroes.
We'll learn their craft and maybe even find some inspiration along the way.
There's a part of you in everything you create, your legacy.
"A Craftsman's Legacy."
[ Horns playing ] So, you're a bit of a jack-of-all-trades, aren't you?
>> I do a lot of different things.
>> Yeah?
>> I teach at the university, and I'm a French-horn player, and I make all these horns that you see around you.
>> They're beautiful.
They're amazing.
How'd you get into it?
I mean, how did you get into playing, I should say, 'cause that's probably where it started, right?
>> I started playing the trumpet in elementary school, and I did that all the way through high school.
Not very well.
And then I discovered the French horn in high school, and it just was a good fit.
>> What was it about the French horn that, I guess, drew you to it?
>> First of all, I liked the sound of it.
>> Okay.
>> And I also liked the music that the horn plays.
And there really is a lot more -- I may be biased about this, but there's a lot more you can do with a French horn that's really fun... >> Yeah?
>> ...than with a trumpet.
>> And how about you?
How did you find your way into it?
>> Well, when I was a small child, my dad took me to the Cleveland Orchestra concerts.
I grew up in the Cleveland area.
>> Okay.
>> And I fell in love with the sound of the French horn, as well.
>> All right.
>> And so I started taking lessons.
>> Just the sound of it?
>> The sound of it.
I love middle voices and the lower voices, and I also liked the solos and the orchestra parts that the horn had.
>> All right.
At what point did you decide that music was your love, and you were going to become a professional musician?
>> It was at the end of high school that I had to make a choice of what I was gonna study, what I was gonna major in as a college student, and I thought, "Give it a chance.
Give it a try."
>> And then what happened after that?
>> I played in the opera orchestra in Detroit, and then I played in the Toledo Symphony for three or four years, and then I decided I needed -- to get a better job, I needed a little more education.
So I came to Bloomington, to Indiana University, to do a master's degree.
>> Were you making horns at that time?
>> I started out putting together horns from pieces of modern horns, but without valves.
So, the old horn doesn't have valves.
That's the difference between the old and the modern horn.
>> Okay.
>> And you can take apart an old horn and take the valves out of it and it sort of plays like the real thing.
And that's what I did in those days.
>> How did you get into the point where you're actually starting to make your own horns, though?
>> When both of us started playing with early-music groups, groups that play on instruments of different periods, it became necessary to really have good instruments, ones that were authentic in their dimensions, and then I had to start learning some serious metalwork and serious design, and do some serious study.
>> You follow vintage techniques, too, correct?
>> I try to.
Some of my machines are run by electricity -- the drawing machine that we use a little bit later, and the lathe.
I don't have an apprentice who can turn a crank to make the lathe go.
>> [ Chuckles ] >> But it's interesting that, in the world of brass instruments, that they sort of have to be made by hand.
Usually the instruments that I'm copying are pretty well-known.
>> Okay.
>> And horn players will know, "This is a really fine instrument, and it fits the bill for this period."
Because what I need to do is cover different periods of music.
Like from 1700 to about 1750, the music of Bach and Handel takes one kind of horn, but the music of the second half of the 18th century, Mozart and Haydn, takes another kind of horn.
>> Oh, okay.
>> And then there are horns from different countries.
There are English instruments and German instruments and French instruments.
>> All right.
Yeah, that makes a lot of sense.
Do you work together on the horns?
>> We do.
He does the bulk of the work.
But having smaller, more delicate hands, I'm able to do some of the finishing work... >> Oh.
>> ...and some of the patient polishing and preparation of the bells, and scraping of solder, and some of the little details that, you know, make the horns almost look like jewelry by the time they go out of here.
>> Sure.
I would think that your horns are probably sold all over the world.
>> I've had a lot of horns go to various European countries, and to Japan, to Australia, South America.
>> Does it make you think about your legacy much?
>> It does.
And these horns will last for a long time.
The originals have been around for 200 and 300 years, so I'm hoping mine will be, too.
>> Sure.
>> That people will take good care of them and play them and use them in concerts and recordings.
But, really, that's part of a legacy.
Those are physical objects.
But there's a more important part of legacy, which is students.
Because I've got 30 years of students who are out there playing the French horn professionally or doing whatever they're doing musically.
And then I have, at this point, three people who've apprenticed with me here.
And so passing things on, I think, is a more important legacy than... than making a horn or playing a concert.
>> Yeah, I would agree with you.
So, how do you see yourself?
Do you look at yourself as a craftsman or as an artist?
>> I think, when I'm pounding on pieces of metal, I'm a craftsman.
>> Yeah?
>> Because that's a tool in your hand and a piece of material and an idea in your head of what you want that material to become.
And so that's just total craftsmanship to me.
But when I'm holding the horn in my hands, then it's a work of art.
But it's also a tool that somebody else uses to make some more art.
>> Sure, sure.
Oh, yeah, yeah, yeah.
>> When we play.
>> Yeah.
>> So, there's an old German saying, it goes, "Kunst ist schoen, macht aber viel arbeit."
And that means, "Art is beautiful, but it's a lot of work."
>> [ Laughs ] >> And it is a lot of work.
>> It sure is.
It sure is.
And I think I'm about ready to get to work.
What do you think?
>> You want to get your hands dirty?
>> Absolutely.
>> Okay, let's go make something.
♪♪♪ >> The natural horn was often used by European nobility to create a signal that would resonate through the countryside during hunts in the 1600s.
The 18th century marked a turning point as it began to be incorporated into classical musical compositions written by composers such as Bach, Mozart, and Beethoven.
With the invention of the valve, the natural horn eventually evolved into the French horn.
Though the instruments have become more sophisticated with time, many of the techniques for making them have remained relatively the same for hundreds of years, and have been passed down from master to apprentice.
Rick and Celeste Seraphinoff's passion for the sound of the original instruments has led them to keep these techniques alive and pass them down to future generations.
Well, this looks like a really nice horn.
>> That's a very old horn.
Yeah, this was made in Paris in about 1820.
>> Now, what kind of horn is that?
>> This is known officially as a French classical orchestra horn.
I thought, instead of trying to make a whole horn, which takes quite a long time, we would work on a restoration project.
This horn has now been restored.
The dents have been removed, and it's been cleaned up so that it's playable, except that it's not complete.
We need to have tuning crooks for the horn.
And you plug the crook in like that, and now we have a complete horn.
>> Oh, I got you.
>> [ Playing scale ] >> Nice.
>> This crook will only play in the key of "G." So, let's say I wanted to play in the key of "F." I would plug in a crook that -- now you can see it's two coils, and it's about a foot and a half longer.
And you'll hear the difference.
[ Playing scale ] And to play in all of the other keys, you would need, oh, 8 or 10 more.
>> So, which one are we gonna make today?
>> I think what we'll do today is make the simple, one-coil "G" crook for the horn.
>> Okay.
>> I think that's something we can pull off in an afternoon.
>> And where do we start?
>> We start by making a tube.
So, what you're gonna do first, here, is take the scriber, hold down the pattern very firmly so it doesn't move, and scribe a line on both sides to make the pattern that you're gonna cut out.
>> Okay.
[ Classical music playing ] ♪♪♪ And since we're gonna match up these sides over a mandrel, we have to be really critical with this, right?
>> They have to really fit exactly.
You stay right on the line, and we'll get exactly the dimensions we need.
This is an old-fashioned, very slow-moving workshop.
>> It's nice.
It gives you time to appreciate what you do.
>> But the box of tools that I have here, my hand tools that I use mostly, are very much like what they would have had.
Okay.
That's beautiful.
>> How's that look?
>> Yeah, that's great.
>> Is that gonna work all right?
>> Okay.
So, now we have a bit of a problem in that this metal is not very malleable.
It's quite stiff.
>> Ahh.
So we're gonna anneal it?
>> Exactly.
>> Awesome.
>> Yeah.
I'll show you the color to which we need to go.
It needs to be a dull red.
>> Okay.
>> Though the difference between dull red and bright red isn't very much, and bright red turns into melting.
>> Not good.
>> Not good.
[ Torch hissing ] See that dull red?
And then I move on immediately, as soon as I reach the dull red.
Okay, so, I'm gonna hand this over to you.
>> Is that all right?
>> Perfect color.
Yep.
[ Torch hissing ] And now I'll do this.
>> All right.
>> And I'll hold it to the end.
Okay.
>> It's good?
>> We now have a soft piece of metal.
And we'll just set it down here on these bricks to cool for just a couple minutes.
This is called a steel mandrel.
It's a tapered steel rod... >> Wow.
>> ...and it has very exact dimensions turned into it on the lathe.
And this is the dimensions of the inside of the tube.
>> Okay.
>> So what we're gonna do is, we're going to start bending this over.
You can do it on that end, and I'll do this end.
And... >> And we're literally just gonna bend this over the mandrel.
>> Right.
And make this into a tube.
So, we'll get the joint to be absolutely as tight as we can get it, take it over to the soldering bench and put it on the firebrick, and then we'll heat it up and do the silver solder joint.
You want to give it a try?
>> Certainly.
♪♪♪ ♪♪♪ ♪♪♪ ♪♪♪ ♪♪♪ >> So, I'll give you the wooden hammer first.
Wooden hammer, burnisher, and a file.
And you can go back and forth between those three.
>> Okay.
♪♪♪ ♪♪♪ ♪♪♪ >> Okay.
That seam is looking good.
♪♪♪ >> Now, this is a pretty crazy machine.
What does it do, exactly?
>> We're actually gonna use it to make a tapered tube.
So, we're gonna put the tube onto the mandrel.
Like that.
>> All right.
>> And then we're gonna draw it through the washer.
>> You're putting a little lubrication on there?
>> A little lubricant.
>> Mm-hmm.
>> And then we'll screw it in to the end.
Okay.
Now we'll just pull it until the end pokes through, and then we'll be certain that everything's in order, and that everything will draw smoothly.
>> All right.
It looks like it's pulling through right now.
>> So, you can turn on the motor.
[ Machine whirring ] >> Oh, that's cool.
>> Perfectly smooth and perfectly round.
But... >> Wow!
>> ...something even cooler that's happening down here is that the tube is getting longer.
So, this tube will end up probably three or four inches longer than it was.
>> Wow, that much?
>> Yeah.
This machine was made about 1979 by my father and myself.
>> So, did you have a picture or something to go by, or did you guys just come up with a design yourself?
>> Well, I had visited some instrument makers and seen similar machines, mostly made by the instrument makers.
And I took photos, and I showed it to my dad, and he said, "Let's do it."
[ Whirring stops ] So, now we have our tube.
So, our next step will be to anneal it again because it's been totally work-hardened, and then fill it with pitch and bend it.
>> And what is that?
>> Pitch is a mixture of asphalt and pine resin.
Because if the tube isn't supported -- it's really thin.
It's only 16/1,000 of an inch, remember -- it totally collapses.
So, now we can start bending.
And I'll bend it around a little bit, and then you can continue the bend.
>> Oh, you're not even using any heat or anything.
>> No, this is done cold.
And we pour the pitch in, and it solidifies, and then you can bend it at any point.
Keep bending.
>> All right.
[ Cracking ] >> And here's our pattern.
You want it to look about like that.
And we'll take it off and compare it to the pattern in just a minute.
>> Okay.
>> But you can do it by eye for the moment.
Yeah, there you go.
>> How's that?
>> Okay, a little more.
See, we want to get it looking like that, so go around a little bit more.
>> Little bit more?
>> Yep.
Until you have just this much.
>> Oh, okay.
>> Yeah, that's what we're looking for.
Okay.
And now let's take it off of there and set it on the bench and compare it to the pattern.
Well, you nailed that the first time.
>> [ Laughs ] Beginner's luck.
>> That's just about perfect.
Wow.
We might just tweak it a little bit like this.
>> So, there's a very specific length to this, right?
>> There is.
This crook, the "G" crook, needs to be exactly 38 inches long.
>> Okay.
>> So what we'll do is we'll measure with a tape measure from the beginning and find the point that we want to cut off.
And we go around the outside.
This is not an exact measurement of length, but it's a comparative measurement that I can reproduce.
>> Oh, okay.
>> And so we find 38 inches and mark it with a pen.
And then we can cut it off at this point.
>> So, now do we have to get the pitch out of it?
>> Right.
And that's done by heating it up and melting the pitch out.
And we can just step into the pitch room where we can do it under an exhaust hood.
♪♪♪ When it all burns away, then we have a clean tube.
[ Metal hisses ] >> So, the pitch has been burned out of this.
>> Mm-hmm.
>> And then it went into the pickling.
And now what's left?
>> What we're going to do is a polishing procedure.
>> So, how do we do that?
>> And the first thing that we do is take one of these finely-sharp scrapers... >> Mm-hmm.
>> ...and you find a sweet spot around the middle or so, and you end up taking long, thin strokes.
>> Oh, real lightly.
>> Very lightly.
Use a very light touch.
And overlapping the previous stroke with the next stroke.
>> And that's taking off very, very little at a time.
>> Very little.
You can't even see a burr.
It's so -- but you can see.
See it's getting shinier?
>> Mm-hmm.
>> But, if you notice, it leaves fine little ridges as you do this.
But the next thing that you would do after you've made these fine lines with the scraper, to get rid of those ridges, you take a little bit of brass polish... >> Mm-hmm.
>> ...and steel wool.
Now, back in the day, they would have used brick dust or pumice powder and a cloth to do this same satin finish that we're going to get now.
And then you just -- again with a light touch, you just rub over all of the scraper marks that you just made.
And see?
It brings it up to a... >> Nice satin.
>> A nice satin finish.
Now, that's a pretty finish, but we want it just a little bit shinier.
And how we go about taking it to the final level of polishing, we take this curved, highly polished burnisher, and we go about the same motion that we used with the scraper.
And as you can see, as I do that, you overlap each previous stroke.
Can you see it getting shinier and glossier as we go?
>> Yep.
Yep.
>> So, that's what has to be done on this entire... >> So it's gonna take a little bit of time.
>> It's gonna take a little bit of time.
But we can work on this while Rick is at the lathe making the tenants for the little pieces that get soldered onto this.
Start out with the scraper.
[ Metal scraping ] And I can see it getting shiny.
>> It sure does.
>> Mm-hmm.
[ Lathe whirring ] ♪♪♪ ♪♪♪ ♪♪♪ ♪♪♪ ♪♪♪ >> I just finished this on the lathe.
This is the part that goes into the socket of the instrument and makes an airtight seal.
>> Oh, okay.
So that goes on the end of this.
And then this piece here does what?
>> This is a reinforcing sleeve that goes over the end of the mouthpipe and just makes it a little bit stronger.
That's another one that was seamed and drawn in the same way.
>> Yep.
And what about this little ring here?
>> That little ring is yet another little reinforcement for the end of the mouthpipe, and it's also very decorative.
>> Ahh.
And this looks like some kind of brace?
>> That is in fact a brace.
And it will go in here after everything else is assembled, making the crook stronger and more rigid.
>> Sure, sure, sure.
>> Mm-hmm.
>> And it looks like we have a last little bit there.
>> And this is the little label, which was made of a little diamond and stamped with the name of the key of the cook.
And this is a "G" crook.
And it's in French.
Sol.
>> [ Laughs ] As in, "Do, re, mi, fa, sol."
>> Yeah, yeah, yeah.
That's awesome.
That's cool.
>> So, this crook speaks French.
>> [ Laughs ] So, how do we put all this together now?
>> Well, we're gonna assemble everything with a soft solder.
The other soldering that we did was hard solder, which is a high-temperature solder.
This is quite a low-temperature solder that consists mostly of tin, with a little bit of silver.
>> And then once this is all together, what's our next step?
>> It's the last step.
>> Yeah?
>> And that is cleaning up the soft-solder joints.
Because when you do soft soldering, you invariably get a little bit of the solder running out the side.
>> Sure, sure.
>> And then Celeste will show you how to scrape away soft solder and then do the final polishing with steel wool and brass polish.
And then we're done.
Plumbers know this as sweat soldering, where you just apply a little bit of solder, and the joint just sucks it right in.
♪♪♪ ♪♪♪ It takes in the flux better.
♪♪♪ Very good.
Wow.
Okay.
[ Metal scraping ] [ Classical music playing ] ♪♪♪ ♪♪♪ [ Music ends ] >> You know, I've not played a horn before.
[ Discordant notes play ] [ Laughs ] I don't think it sounded the same.
>> Well, it totally worked.
>> Man, this is just amazing.
This is a beautiful piece.
Beautiful.
Thank you so much for having me out.
>> Oh, we had a great time.
Thank you.
>> I really appreciate it.
Thank you.
>> It looks good on you.
>> Oh.
[ Laughs ] Thanks.
Rick and Celeste were so gracious with their time and their talents.
And once again, I've proven to myself I need to stick with the drums.
♪♪♪ ♪♪♪ ♪♪♪ ♪♪♪ ♪♪♪ >> There's more than one way to leave a legacy.
For some, it means plaques, monuments, and halls of fame.
But for others, legacy comes from a place more simple.
>> You just snip off the ends.
♪♪♪ Okay, so, we're building a tepee shape.
>> The Ford F-150, a proud supporter of "A Craftsman's Legacy."
♪♪♪ >> To discover more about "A Craftsman's Legacy" and the craftsmen we feature, please visit our website.
And you can also follow us on social media through Facebook, Twitter, and Instagram.
Support for PBS provided by:
A Craftsman's Legacy is presented by your local public television station.
Distributed nationally by American Public Television